What’s an ERP System in Manufacturing? A Complete Guide for Modern Factories
Manufacturing today is no longer confined to putting products together it encompasses systems integration, automation of tasks, and smooth processing from raw materials to customers.
As supply chains become more complex and customers demand speed and accuracy, manufacturers are increasingly able to lean into technology.
And this is where ERP systems market themselves. ERP software assists these manufacturers in unifying, streamlining, and automating major processes like inventory control, procurement, production planning, logistics, accounting, and regulatory compliance.
Because no two manufacturing settings operate in exactly the same manner, many manufacturers actually have custom ERP software development carried out to fit into their own unique workflows, production models, and industry specific needs.
These bespoke systems provide a much broader choice in terms of control, integration, and scalability that off-the-shelf solutions simply cannot offer, especially in environments that call for high precision or stringent regulation.
This guide shall walk you through what ERP in manufacturing really entails, the important modules that constitute it, why customization has to be taken into account, and how it seeks to enhance performance on and off the shop floor.
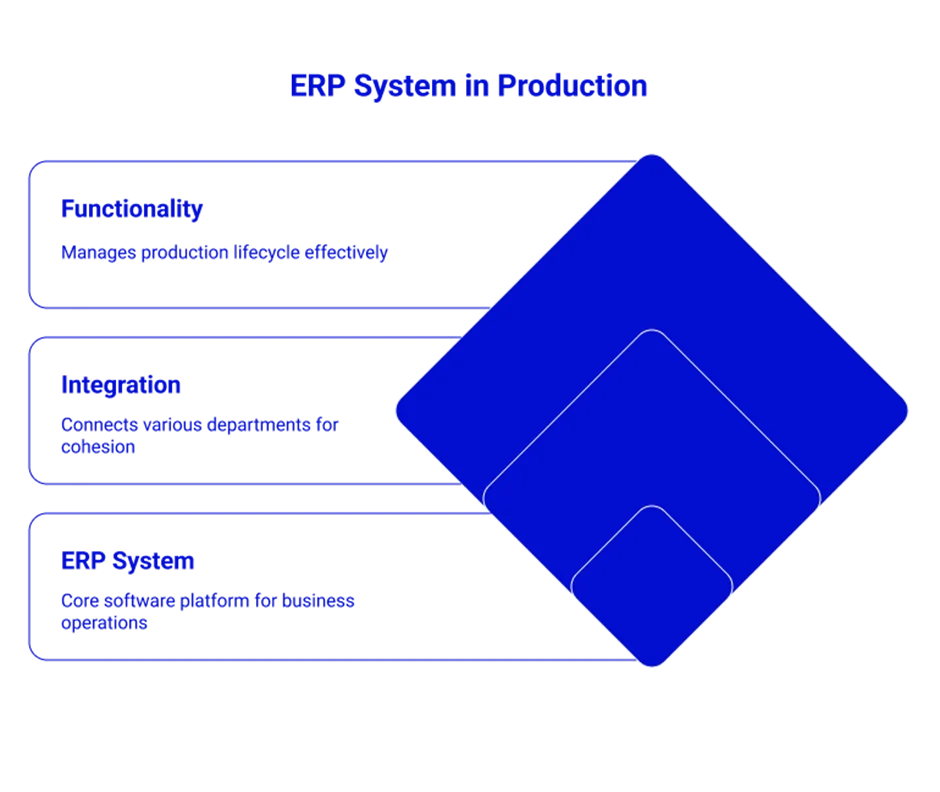
What’s an ERP System in Production?
Production ERP Systems are integrated software platforms that offer an integrated view of the core business and production operations.
Such software connects departments such as procurement, inventory, production, sales, finance, HR, and compliance, and more, to give a cohesive view to the organization.
Manufacturing ERPs, instead, have been designed to fulfill the intricate nature of a production lifecycle.
From forecasting raw material needs to scheduling production lines and even tracking output quality, ERP software gives visibility and control across every dimension of manufacturing.
Purpose of ERP in Manufacturing:
- Track raw materials and monitor real time usage.
- Manage inventory across warehouses and production lines.
- Plan and schedule production based on order demand and capacity.
- Ensure compliance with regulatory and safety standards.
- Integrate finances with operations for accurate cost tracking.
With everything stored in a central data repository, ERP platforms remove the silos and speed up decision making, adjust operations in real-time, and cut down on operational waste.
Core Modules of a Manufacturing ERP System
To truly support end-to-end operations, a manufacturing ERP system typically includes a set of interlinked modules. Each of these modules focuses on a specific area of the production process:
1. Bill of Materials (BOM) Management
Defines the components, quantities, and workflows needed to build a product. Supports multi level BOMs for complex assemblies.
2. Inventory & Warehouse Control
Tracks raw products, WIP (Work in Progress), and finished goods across multiple places. Supports real-time inventory levels, batch tracking, and barcode/RFID integrations.
3. Production Planning & Scheduling
Helps manufacturers plan capacity, align production with demand, and minimize idle time. Automates scheduling based on workforce availability and machine capacity.
4. Shop Floor Control & Monitoring
Provides live dashboards of machine activity, work orders, and job status. Helps track operator efficiency, downtime, and overall equipment effectiveness (OEE).
5. Supply Chain & Vendor Management
Streamlines procurement, purchase orders, vendor contracts, and inbound logistics. Enables just-in-time inventory management and cost optimization.
6. Order Management & Invoicing
Handles sales orders, delivery tracking, returns, and invoicing. Ensures that consumer orders are fulfilled successfully and as they should be.
7. Quality Control & Compliance Tracking
Automates quality checks at various stages of production. Helps ensure compliance with ISO standards, industry certifications, and safety regulations.
Each module works in harmony to create a digitally connected manufacturing environment that is agile, responsive, and data driven.
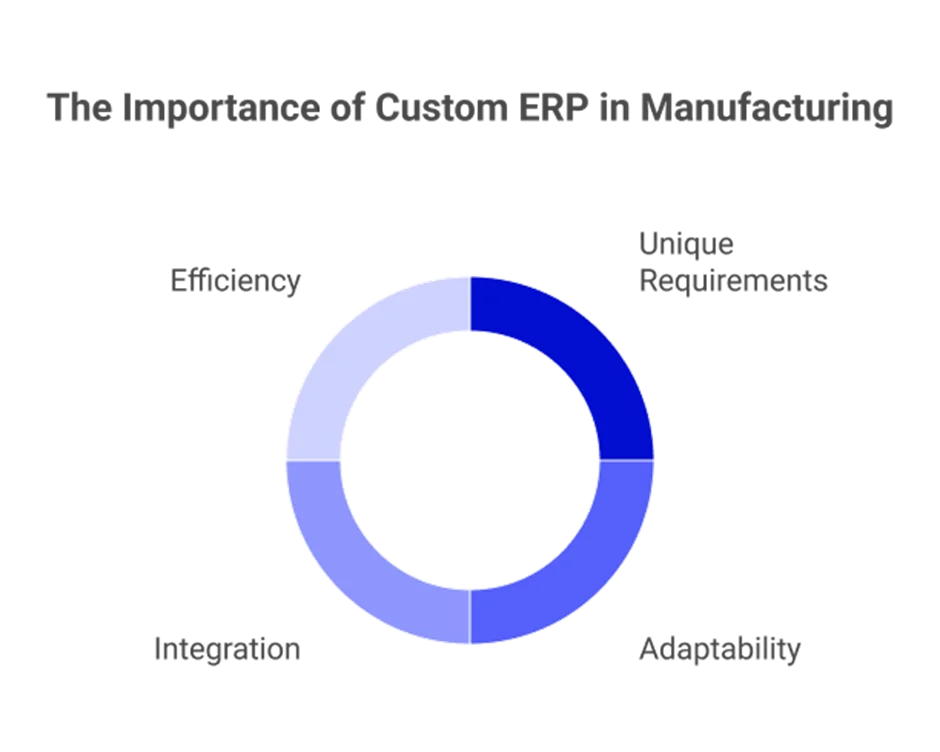
Why Custom ERP Development Matters for Manufacturing
While off-the-shelf ERP solutions offer a range of features, they often fail to meet the unique requirements of modern manufacturing.
Every factory has its own mix of machinery, supply chain models, production workflows, and regulatory constraints.
Rigid ERP templates can limit adaptability, force unnecessary workarounds, or fail to integrate with legacy systems already in use on the shop floor.
Common limitations of generic ERPs:
- Inability to handle specialized workflows (e.g., batch vs. discrete manufacturing)
- Lack of support for industry specific compliance (e.g., FDA, ISO 9001)
- Limited integration with IoT devices, PLCs, or MES platforms
- High cost of customization and upgrades
This is why many factories invest in tailored ERP software development to design systems that work exactly the way their operations require.
Custom ERP solutions not only match existing processes but can also future-proof the organization for scale, innovation, and resilience.
Benefits of ERP in Manufacturing
When implemented correctly, ERP systems can be transformative for manufacturing operations. Here are some of the key benefits:
Improved Efficiency
By automating routine tasks like data entry, procurement, and scheduling, ERP systems reduce manual workloads and minimize human error.
Better Production Planning
Manufacturers gain real time insights into material availability, machine capacity, and labor allocation resulting in fewer delays and better on-time delivery rates.
Inventory Optimization
Track inventory in real time, set reorder points, and avoid both stockouts and overstocking. This leads to better cash flow and space utilization.
Enhanced Quality Control
In built QC modules allow manufacturers to identify and resolve quality issues early in the production cycle, reducing rework and scrap rates.
Stronger Forecasting & Decision Making
Centralized data enables predictive analytics for demand planning, maintenance scheduling, and financial forecasting.
Ultimately, ERP systems empower manufacturers to become more agile, reduce waste, and deliver better products faster and more cost effectively.
Challenges and How to Overcome Them
Like any major digital transformation, ERP implementation comes with its own set of challenges. Being aware of these pitfalls can help manufacturers plan better and avoid costly mistakes.
Common Challenges:
- High Upfront Investment: ERP systems can require significant capital outlay, especially for custom solutions.
- Complex Implementation Cycles: Integrating ERP across departments requires time, coordination, and strong leadership.
- Resistance to exchange: Employees can be hesitant to adopt new systems, particularly if education is missing.
- Integration with Legacy Systems: Connecting new ERP platforms with older machinery or databases can be technically complex.
How to Overcome These:
- Start with a clear roadmap and phased rollout strategy.
- Involve key stakeholders and quit-customers from the start.
- Prioritize training and change management.
- Choose experienced ERP development partners who understand both tech and manufacturing.
Working with a knowledgeable ERP software development partner helps manufacturers navigate these challenges, ensuring the solution fits both technical and business needs now and in the future.
Conclusion
The manufacturing companies have no optional ERP systems anymore; they have become an absolute necessity.
As it moves toward smart factories, just in time production, and real time analytics, ERP software acts as the system for agility and scalability.
But, of course, not all ERP systems were built the same. The best ROI is offered by a custom ERP solution tailored to align with the unique environment of production and long term growth plan of a factory.
By integrating data, optimizing workflows, and enhancing the visibility of the value chain, an ERP platform allows manufacturers to reduce costs, improve product quality, and react multiple times to market changes.
In a competitive environment where efficiency matters, an ERP built especially for your manufacturing process may be the one to bring you from lagging behind to leading the market.